FCASTANEDA (Talk | contribs) |
|||
Line 1,482: | Line 1,482: | ||
window.onload = function(){ | window.onload = function(){ | ||
//alert(teamMembersPhotosArray.toString()); | //alert(teamMembersPhotosArray.toString()); | ||
− | generate_header(" | + | generate_header("Hardware", "10%", "5%", "https://static.igem.org/mediawiki/2021/9/9f/T--TecCEM--FotoEquipoTexem.jpg", "#CDECA9" ,"#45ACFF", "white"); |
var numOfBubbles = 6; | var numOfBubbles = 6; |
Revision as of 00:47, 22 October 2021
Hardware
Objective
A quartz crystal microbalance (QCM) for everyone.
Microplastics are a huge problem and many researchers and even some iGEM Teams are trying to put a stop to them. However, have you heard about Endocrine Disrupting Chemicals? If not, don’t feel bad, many people including regulatory agencies from all around the world have overlooked them. Endocrine Disrupting Chemicals or EDCs are dangerous compounds that come from many sources but are mostly associated with the degradation of certain plastics and its manufacturing processes. They may even be found in drinkable water, so we are exposed to them on a regular basis. Besides, their detection is a challenge due to their characteristics: they are too small and there are too many. In addition, they are difficult to eliminate from water and accumulate in the organism that consumes them. EDCs are related to several diseases that range from metabolic and hormonal health issues to even cancer. The idea is to detect them and even eliminate them.
Our biosensor has 2 main areas:
-
The biological, where we depend on a protein to encapsulate the EDC’s and help the biosensor to do the micro -measure.
-
For the engineering part, it was needed to build a casing that would protect our QCM, while making it easier to do the measuring and to make a circuit in order to have a functional device.
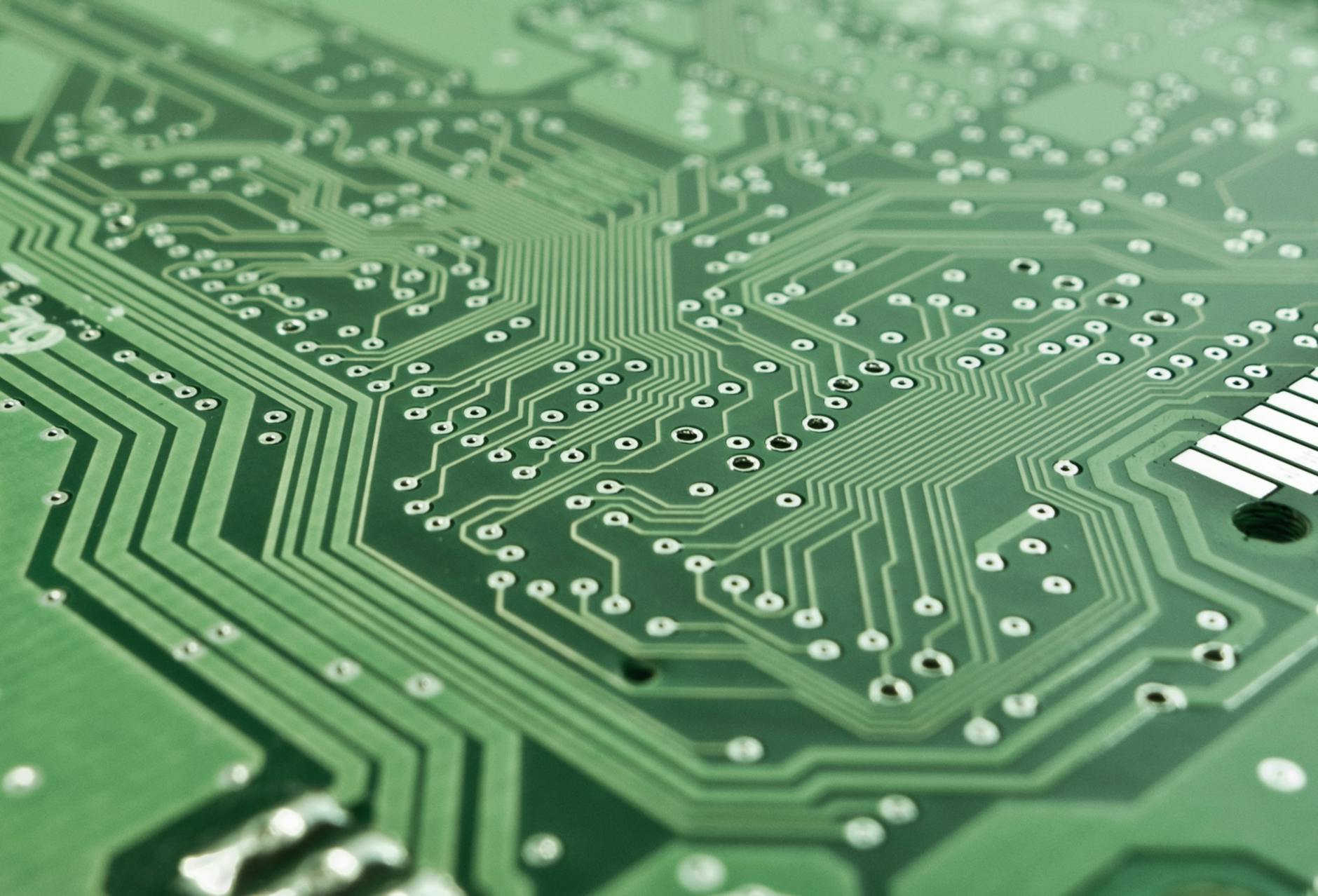

Final product
Here are the 3D printed parts of the biosensor (Figure 1) and later they were assembled with an epoxy resin (Figure 2). Besides, it is shown the base to ensure that quartz crystal was fixed to its position (Figure 3), to avoid measurement deviations or leaks due to water flow over its surface.
Figure 1. Casing of biosensor

Figure 2. Assembled casing biosensor

Figure 3. Base that holds quartz crystal

Figure 4. Render of assembled casing
To achieve the previous results, fusion 360 software was used, in which the electronic components were placed, to ensure that the space would be sufficient and thus, avoid material waste. Below is the virtual model (Figure 4 and 5), once approved, we proceed with the 3D printings.

Figure 5. Lateral view of casing, all the electronic components are inside.

Figure 6. Final model.
Assembled model is shown (Figure 6).
Main components
First of all, it was necessary to choose a microcontroller for the development of this quartz crystal microbalance. One solution was Arduino Nano, which is a microcontroller board, it has a wide range of applications and is a major microcontroller board because of its small size and flexibility. Some of their main features are: 6 PWM pins among the digital pins and it also supports different ways of communication, such as Serial Protocol, I2C Protocol and SPI Protocol. However, to measure the frequency of a signal, it has a measurement limit of 6 MHz.
For that reason an alternative was investigated, which was Teensy 4.1 features an ARM Cortex-M7 processor at 600 MHz, with an NXP iMXRT1062 is a cross- over processor, which has the functionality of a microcontroller, at the speeds of a microcomputer. Which is perfect for when you need tons of flash, RAM and to crunch IOTs of data. It is capable of measuring up to 25 MHz, so it is excellent for these kinds of applications.
To move the flow, two pumps were used, whose motors are RS-360SH. They have an operating range of 3-9 volts, and need a current of 2A approximately. In order to properly control them, it is necessary to have a H bridge, in this case, we decided to use a L298N. It is an integrated monolithic circuit, it is a high voltage, high current dual full bridge driver designed to accept standard TTL logic levels and drive inductive loads such as relays, solenoids, DC and stepping motors.
Finally, the most important thing was to develop a circuit capable of generating the frequency required by the crystal, so we found different modules, the main criterion was the cost, some of them were up to 50 dollars due to the limited availability, but the selected one cost less than 10 dollars, which was an excellent decision. This module already has a certain degree of complexity, so its programming is not so simple, it requires a library that simplifies the code a little and to find the right forums to solve their main problems. AD9833 is a DDS signal generator, which stands for direct digital synthesis. This feature gives it quite acceptable properties, such as output frequencies up to 12.5 MHz, a resolution frequency of 28 bits, which translated is 0.1 Hz, and it is powered with 2.3 to 5.5 V. It is capable of generating square, sinusoidal and triangular signals. All specification sheets are presented in the following folder:
Also, below are the plans with their respective measurements for the 3D printed parts, so it can be replicated by anyone
In the same way, the exploded view is shown with the main components required, as well as their quantity.
The easiest way to explain the assembly and how to replicate it successfully is through a video, which was also made with the help of Fusion 360.
Real model components explanation is below
Finally, the costs for the development of the quartz crystal microbalance and where they were acquired (Table I).

In order that the complete circuit can be recreated, electronic diagrams with all the necessary connections are included. Remembering that Teensy can be used for higher frequency crystals, such as 10 MHz. And if the crystal is 5 MHz or lower, it is recommended to use Arduino Nano.
The above diagram is shown physically (Figure 7).
Figure 7. Electronics circuit plate

Figure 7. Electronics circuit plate
At last, the electronic circuit device totally assembled (Figure 8)

Figure 8. Electronics circuit complete
3D Printing
It was used 1.75mm Zortrax Z-abs filament for a 3D printer model M200 (Figure 9)

Figure 9. Zortrax M200 3D printer,
available at ITESM CEM
All the files are in "stl" format ready to be sent to the 3D printer. They are stored in the following folder.
Or if you are familiar with Fusion 360, you can create a copy of the complete assembly and make any modifications you require at the following link:
Process
First, a research on a tool capable of measuring micrograms was carried out, different articles were found ("Oscillator for biosensors based on quartz crystal microbalance (QCM)” [1], "New Approach to a Practical Quartz Crystal Microbalance Sensor Utilizing an Inkjet Printing System" [2]). With further research we found some circuits that were taken as a starting point for our own. Subsequently, we had to be able to generate the signal at the desired frequency, the AD9833 was found. Once acquired all the programming was done in Arduino to functionalize it, a circuit was assembled to increase or decrease the output frequency, change the type of signal (square, sinusoidal, triangular). Then we sought to understand the physical principle, so we bought commercial crystal oscillators of 4 MHz, such as those used in wristwatches, radios, etc.. We analyzed the behavior at the input and output of the crystal using an oscilloscope, also a function generator was used to vary aspects such as amplitude and compare it with the results of the AD9833 in the oscillograph. These crystals worked and the expected physical phenomena occurred, but due to its characteristics did not have the required resolution, so a package of quartz crystals for liquid biosensing in OpenQCM of 10 MHz was requested and a Teensy 4.1 was purchased, since the Arduino Nano used was not capable of measuring that frequency.
We continued with the CAD designs of the quartz crystal microbalance model that we wanted to implement, for which we used Fusion 360. It was designed so that all the electronic components are housed inside the casing and on the outside there are the parts that are directly used for the measurement, such as the 2 mL microtubes for the inlet and outlet, and the quartz crystal isolated so that the flow can only make contact on one of its surfaces. The prints for the 3D housing were made on a Zortrax M200 machine with ABS as filament.
We looked for different pumps to perform this work, and we opted for ones capable of working with 3 to 9V and 2A of current. To control the drive times and the direction of the motors, an H-bridge was used, which is in module L298n.
Initially, a submersible pump was used and tests were made to check if it could transfer the water from one container to another. However, due to the design it was necessary to make an adjustment and change the pump.
After several tests and making everything work, we proceeded to assemble the complete circuit, for which a phenolic plate was used.
If the product is to be commercialized, the best option is to print the circuit on a PCB, this is easily done once all the connections are defined, for this you can use specialized software such as Proteus, or online tools such as EasyEDA.
Everything was integrated within the interface programmed in Python, the objective of this was always to provide the user with a simple and effective way to perform the measurements. Among the options provided by the application is to select the port to which the electronics were connected, the crystal frequency specified by the manufacturer and a tool to calibrate the applied frequency, the total measurement time and the time delta between each measurement, as well as the opportunity to select whether it is a continuous flow, paused or manual, the latter provides the opportunity to perform measurements using micropipettes. All this is included in a friendly interface and the results are plotted in real time, the option is provided to download the graph and all measured data in txt format for further analysis.
Finally, we proceeded to perform the measurements to characterize the sensor. Twelve known masses were used, which were weighed on an analytical scale (name them later). The frequency of the crystal was obtained with each mass and without them, so that the frequency difference was calculated, with this data it was possible to obtain the linear equation that models the relationship between mass and frequency. Here you can see how to integrate hardware and software:
Quartz crystal
This is probably the most important component, since its quality when manufactured (and therefore its cost) is directly related to the resolution achieved. It is for this reason that we decided to buy a package (10 pieces) of 10 MHz quartz crystals (Figure 10) with OpenQCM company, specialised in liquid biosensing [3].

Figure 10. 10 MHz quartz crystal package
These cost a total of 219 euros (255 USD). Its characterization is shown below, which is available on the aforementioned page (Fig 11 and 12).

Figure 11. Technical specifications part 1

Figure 12. Technical specifications part 2
References
[1] Montagut, F., Yeison, J., García N., Jiménez, Y., Mach C., Montoya, A., Torres, R. & Arnau, A. (2011). Oscilador para biosensores basado en microbalanza de cristal de cuarzo (QCM). Facultad de Ingeniería Universidad de Antioquia, (61),114-122. ISSN: 0120-6230. Available at: https://www.redalyc.org/articulo.oa?id=43023590012
[2] Fuchiwaki, Y., Tanaka, M., Makita, Y., & Ooie, T. (2014). New approach to a practical quartz crystal microbalance sensor utilizing an inkjet printing system. Sensors 2014, 14, 20468-20479; doi:10.3390/s141120468
[3] OpenQCM. (2021). 10 MHZ QUARTZ SENSORS BOX FOR LIQUID BIOSENSING- 10 PIECES [Online]. Available at: https://store.openqcm.com/10-mhz-quartz-sensors-box-for-liquid-biosensing-10-pieces/